Cellulose is the main constituent of plant fiber making it the most abundant organic compound on Earth [1]. Owing to its excellent mechanical properties, natural abundance, biodegradability, low cost, and renewability, cellulose is regarded as a promising eco-friendly alternative for traditional petroleum-based polymers with applications in a variety of fields such as aerogels, hydrogels, high tenacity rayon or transparent films [2].
One of the challenges in the manufacturing of cellulose-based products is the high melting point of cellulose which makes it impossible for it to be melted without decomposition. Thus, shaping cellulose materials generally requires dissolution of the cellulose polymer and regeneration. Regenerated cellulose fibers for example are dry jet wet spun from ionic liquid solutions.
It is thus essential to understand the nanoscale structural changes taking place along the production process. Small and wide angle X-ray scattering measurements are an ideal probing technic in this context that can reveal the evolution of the microstructure and of the crystalline order. Moreover, the mechanical properties of the majority of the cellulose-based products are strongly dependent on the nano and micro-scale structure of the interface between cellulose surfaces and other materials, in particular in the wet state as the joints are developed and then consolidated during drying [4]. Grazing incidence small angle X-ray scattering (GISAXS) is a versatile tool for characterizing nanoscopic objects at buried interfaces, surfaces, or in thin films.
In this article you will discover how SAXS and WAXS measurements have been used to:
- Uncover the structural changes that take place during the drying process of cellulose beads swollen with different water/ethanol mixtures and containing different cellulose concentrations,
- Determine the variations in crystallinity of regenerated cellulose fibers produced with different draw ratios.
Nanostructural evolution of cellulose beads during drying investigated by SAXS
Recently, a group of researchers from the Jülich Centre for Neutron Scattering and Biological Matter and KTH Royal Institute of Technology have performed an in-depth study of the nanostructure evolution on a model system composed of regenerated cellulose beads. The aim has been to investigate the influence of the cellulose concentration and the nonsolvent type and concentration [2,3]. The cellulose beads have been fabricated by precipitating a solution of cellulose/lithium chloride (LiCl)/N,N-dimethylacetamide (DMAc) into a nonsolvent (ethanol or water). Subsequently, time-resolved SAXS measurements performed on both water and ethanol swollen beads have been used to track the nanoscale structural changes that occur during drying. Based on the shape of the SAXS curves three drying regimes can be defined for the water-swollen beads in comparison with only two regimes for the ethanol-swollen counterparts.

Fig. 1 (a)-(d) Evolution of two characteristic length scales (Rg1 and Rg2) and two dimensionality parameters (s1 and s2) as a function of drying time and nonsolvent. (e) Graphical illustration of the structural evolution during nonsolvent evaporation. Credit: ACS Nano, 2020, DOI: 10.1021/acsnano.0c00171.
In order to quantitatively evaluate the structural changes that take place during the drying process, the data has been fitted with a Guinier-Porod model. Monitoring the evolution of some of the fitting parameters as a function of drying time allows for a better understanding of the structural changes that occur in each regime. From basic knowledge of cellulose structure and the order of magnitude, the two characteristic length scales, Rg1 and Rg2, can be attributed to the size of the cellulose monomer and the size of an elongated aggregate structure (see Fig. 1 (e)). The shape of the corresponding scattering objects is characterized by the two dimensionality parameters s1 and s2:
- spherical symmetry s1 = s2 = 0,
- cylindrical objects s1 = 1, s2 = 0,
- lamellae with equal width and length s1 = 2, s2 = 0. It is thus possible to describe the structural evolution during the evaporation of the nonsolvent by interpreting the values of all the parameters in each regime (displayed in Figs. (a)-(d)).
Water- swollen beads evolution (Figs. 1 (a) and (c))
Regime I (evaporation time < 18 min)
Before drying starts the cellulose monomers present a lamellar stacking structure of size in the order of 1 nm (corresponding to Rg1) combined with larger elongated structures with the shortest size of approximately 3 nm (related to Rg2).
Regime II (evaporation time 18 – 28 min)
The rapid decrease of both s1 and s2 to 0 points towards the formation of structures with spherical symmetries. These larger structures are formed by the merging of the already existing elongated aggregates as indicated by the increase in both Rg1 and Rg2.
Regime III (evaporation time >28 min)
The objects with smaller characteristic sizes form rod-like structures with an approximate size of 0.5 nm while the larger ones maintain spherical symmetry.
Ethanol- swollen beads evolution (Figs. 1 (b) and (d))
Regime I and III
A similar structure as the water-swollen beads is observed in the swollen state (regime I). It is composed of staked monomers and larger elongated structures. Furthermore, no major structural changes are observed throughout the evaporation process.
Crystalline order evolution of cellulose beads during drying investigated by WAXS
WAXS measurements have been used to investigate whether crystalline order is formed during the evaporation process. For water-swollen beads, three peaks are visible in the spectra presented in Figs. 2 (a) and (b): the scattering peak from water (q = 20 nm-1) and two peaks assigned to the (110) (q = 8.8 nm-1) and (110) (q = 14.6 nm-1) crystallographic planes of cellulose II structure. As a function of evaporation time, the water peaks decrease significantly in intensity, as expected, while the cellulose peaks only appear at the beginning of regime II (18 min) and continue to increase in intensity during the rest of the drying process. A peak shift along the (110) direction has been observed (Fig. 2 (a)) indicating that at the beginning of regime II a cellulose II hydrate structure forms followed by a continuous transition to cellulose II structure.
For ethanol swollen beads on the other hand no crystalline structures are formed during drying. In this case, only an intensity change of both the ethanol (q = 15.5 nm-1) and cellulose (q = 14.6 nm-1) peaks is observed throughout the evaporation of the nonsolvent.

Fig. 2 (a), (b) WAXS curves recorded at different times during drying process of water and ethanol swollen beads respectively with 1.5 wt% cellulose concentration. Credit: ACS Nano, 2020, DOI: 10.1021/acsnano.0c00171.
Furthermore, by performing SAXS/WAXS experiments on cellulose samples swollen with different water/ethanol mixtures and containing different cellulose concentrations it has been possible to design a phase diagram (Fig. 3) that enables a straightforward prediction of the drying behavior of regenerated cellulose.
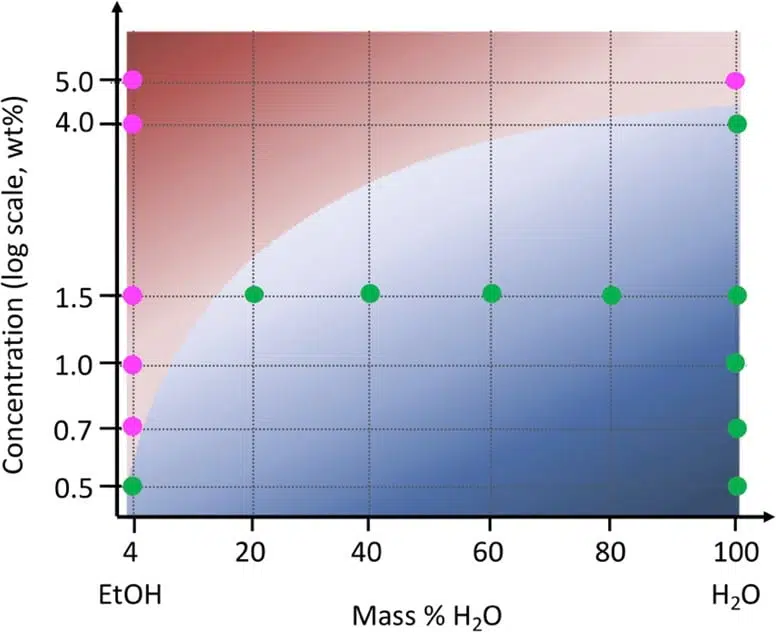
Fig. 3 Phase diagram showing the structural evolution during drying of cellulose bead as a function of nonsolvent mixture. Magenta points correspond to a two-step drying process with no change in the cellulose structure, while green points represent a three-step drying process including a sharp structural change. Credit: ACS Nano, 2022, DOI: 10.1021/acsnano.1c09338.
Crystallinity of regenerated cellulose fibers
The crystallinity of regenerated cellulose fibers has been recently investigated by a group of researchers from the University of Bari, Aalto University, the Institute of Crystallography and Lund University [5]. Polymers crystallization in general is associated with only a partial alignment of molecular chains through cooling, mechanical stretching, or solvent evaporation. The result is thus a mixture of amorphous and crystalline domains the ratio of which can be tuned by processing parameters such as the draw ratio.
The influence of the draw ratio on the crystallinity of regenerated cellulose fibers has been assessed through wide angle X-ray scattering measurements. In order to accurately determine the degree of fiber crystallinity (ϕc), i.e. the volume fraction of the crystalline domains, WAXS patterns have been decomposed into individual amorphous and crystalline contributions as exemplified in the inset of Fig. 4. As a function of increases draw ratio, ϕc increases sharply up to DR = 5 and saturates to a value of ϕc = 0.6 ± 0.05 for all higher draw ratios. This behaviour correlates with the evolution of the mechanical properties of fibers produced with different DRs. The tensile strength has been seen to increase by approximately a factor 2 at low draw ratios (DR < 5) followed by a continuous but slower increase at higher draws [6].

Fig. 4 Fiber crystallinity obtained at different draw rations (DR). (inset) Individual contributions to the WAXS pattern of the crystalline and amorphous domains recorded on a DR 15 sample. Credit: IUCrJ, 2022, DOI: 10.1107/S205225252200570X.
Conclusions
The drying kinetics of cellulose beads containing various cellulose concentrations and swollen in different nonsolvent water/ethanol mixtures have been studied in detail through SAXS and WAXS measurements. These results demonstrate the different structural evolutions during drying depending on the cellulose concentration and the non-solvent used. Moreover, WAXS measurements proved to be an excellent tool to probe the crystallinity level of regenerated cellulose fibers produced with different draw ratios. This work offers valuable information about the mechanisms that occur during the drying of regenerated cellulose and the influence of processing parameters. These insights are crucial in the manufacturing process of numerous cellulose-based products.
References and further reading
The research was originally published in the following articles:
[2] Li, Hailong, Margarita Kruteva, Martin Dulle, Zhen Wang, Katarzyna Mystek, Wenhai Ji, Torbjörn Pettersson, and Lars Wågberg. “Understanding the Drying Behavior of Regenerated Cellulose Gel Beads: The Effects of Concentration and Nonsolvents.” ACS nano 16, no. 2 (2022): 2608-2620.
[3] Li, Hailong, Margarita Kruteva, Katarzyna Mystek, Martin Dulle, Wenhai Ji, Torbjörn Pettersson, and Lars Wågberg. “Macro-and microstructural evolution during drying of regenerated cellulose beads.” ACS nano 14, no. 6 (2020): 6774-6784.
[5] Gentile, Luigi, Herbert Sixta, C. Giannini, and U. Olsson. “A novel X-ray diffraction approach to assess the crystallinity of regenerated cellulose fibers.” IUCrJ 9, no. 4 (2022).
[1] Wang, Sha, Tian Li, Chaoji Chen, Weiqing Kong, Shuze Zhu, Jiaqi Dai, Alfredo J. Diaz et al. “Transparent, anisotropic biofilm with aligned bacterial cellulose nanofibers.” Advanced Functional Materials 28, no. 24 (2018): 1707491.
[2] Li, Hailong, Margarita Kruteva, Martin Dulle, Zhen Wang, Katarzyna Mystek, Wenhai Ji, Torbjörn Pettersson, and Lars Wågberg. “Understanding the Drying Behavior of Regenerated Cellulose Gel Beads: The Effects of Concentration and Nonsolvents.” ACS nano 16, no. 2 (2022): 2608-2620.
[3] Li, Hailong, Margarita Kruteva, Katarzyna Mystek, Martin Dulle, Wenhai Ji, Torbjörn Pettersson, and Lars Wågberg. “Macro-and microstructural evolution during drying of regenerated cellulose beads.” ACS nano 14, no. 6 (2020): 6774-6784.
[4] Li, Hailong, Stephan V. Roth, Guillaume Freychet, Mikhail Zhernenkov, Nadia Asta, Lars Wågberg, and Torbjorn Pettersson. “Structure development of the interphase between drying cellulose materials revealed by in situ grazing-incidence small-angle X-ray scattering.” Biomacromolecules 22, no. 10 (2021): 4274-4283.
[5] Gentile, Luigi, Herbert Sixta, C. Giannini, and U. Olsson. “A novel X-ray diffraction approach to assess the crystallinity of regenerated cellulose fibers.” IUCrJ 9, no. 4 (2022).
[6] Asaadi, Shirin, Michael Hummel, Patrik Ahvenainen, Marta Gubitosi, Ulf Olsson, and Herbert Sixta. “Structural analysis of Ioncell-F fibres from birch wood.” Carbohydrate polymers 181 (2018): 893-901.
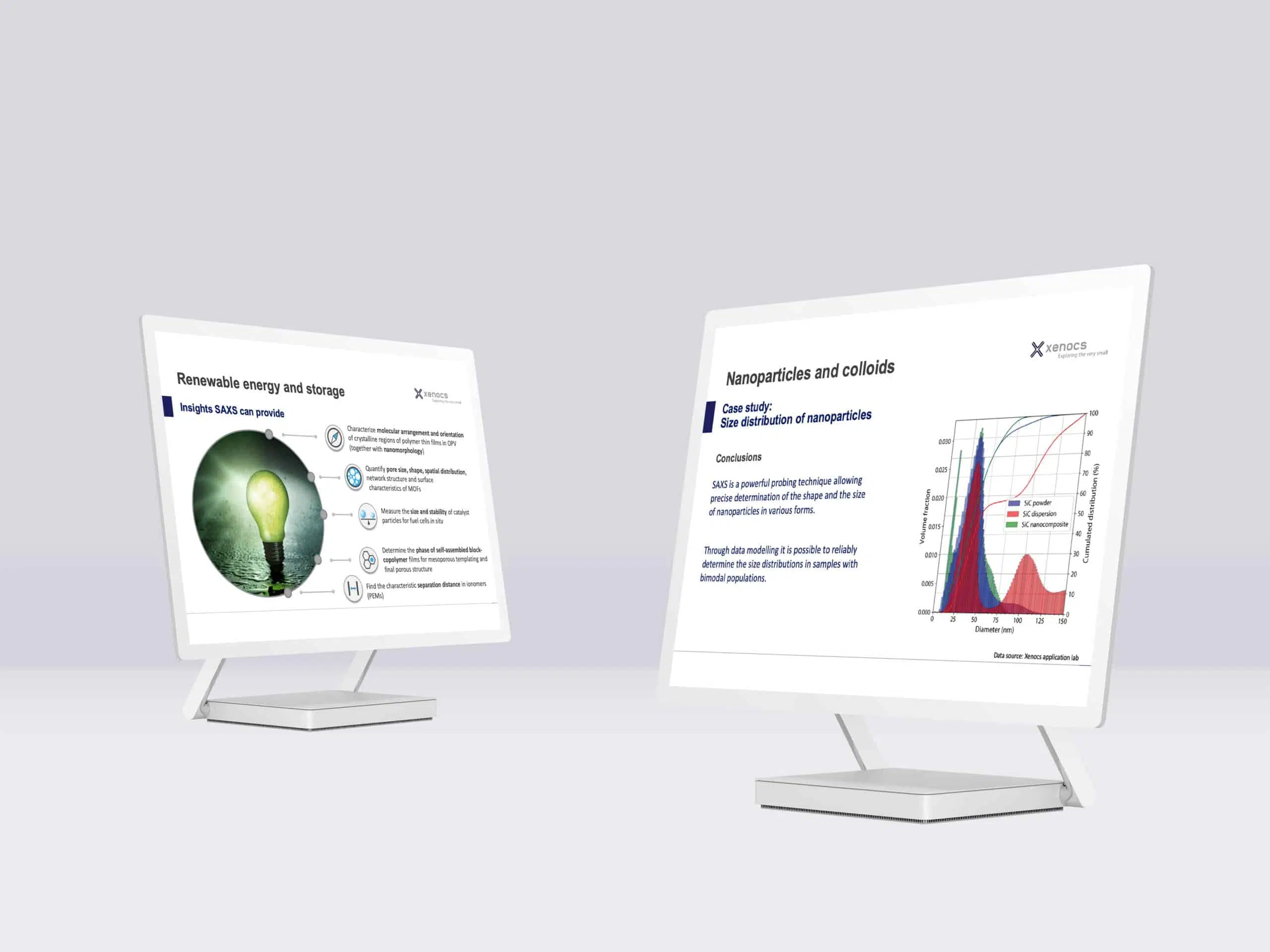